Ship design isn’t just drawing a boat; it’s a complex, multi-stage process that refines an idea into a seaworthy reality. Unlike mass-produced vehicles, ships are bespoke creations tailored to specific missions and optimized for resource use.
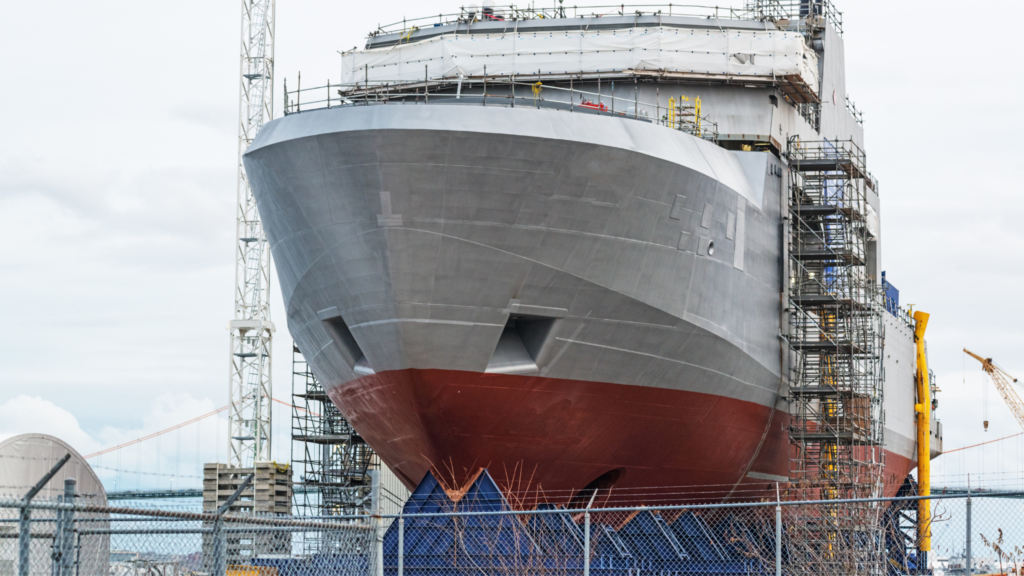
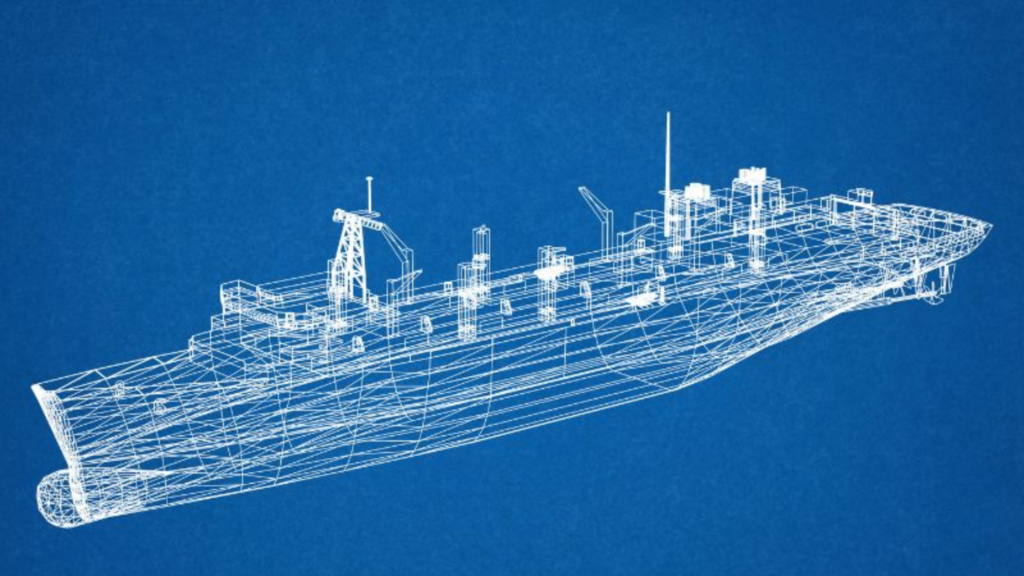
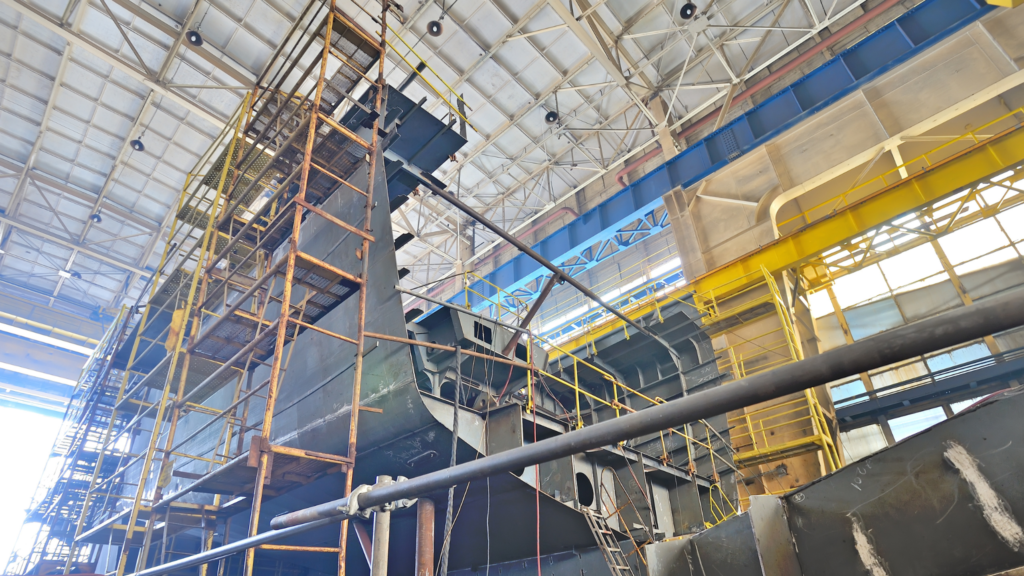
1. Concept Design: The Spark of an Idea
This initial phase identifies the vessel’s operational requirements, like cargo capacity (deadweight tonnage or TEU for cargo ships) or passenger numbers and amenities. Voyage specifics like speed, range, and routes are also defined. From this, a preliminary design emerges, outlining hull form, cargo stowage, stability criteria, propulsion, and essential equipment.
This design undergoes a techno-economic evaluation, assessing its technical and economic feasibility. The technical assessment checks for safety, integrity, and performance against benchmarks, considering factors like buoyancy, stability, structural strength, maneuverability, and environmental compliance. The economic assessment compares construction and operational costs against budget limits. If costs exceed limits, the design is refined and re-evaluated until a cost-effective, technically sound solution is found. Naval architects are heavily involved in this optimization process, leveraging computational resources to evaluate design metrics.
2. Basic Design: Setting the Course
Once the concept design is approved, it moves to basic design, where major aspects become largely irreversible. This phase solidifies hull form, key dimensions, weights, stability, tankage, structural design, space arrangement, hydrodynamics, propulsion systems, electrical distribution, and safety features.
Basic design builds upon the concept, requiring significant input from naval architects, alongside mechanical, electrical, structural, and materials engineers. The basic design stage’s scope includes virtual models, material listings, advanced general arrangements, major structure drawings, global load and strength calculations, stability and seakeeping analyses, and integration of electrical, piping, and HVAC systems. Design adherence to safety regulations is crucial. Design bodies or shipyard design offices typically carry out this phase. Most deliverables require validation from a classification society.
3. Detailed Design: Fine-Tuning the Machine
Detailed design refines the outcomes of basic design. General arrangements and tankages are finalized based on tonnage, stability, and strength considerations. Structural drawings are updated with precise details for every element, including welds and material specifications. Extensive structural analysis, often using Finite Element Analysis (FEM), assesses load behavior, with revisions made until satisfactory strength is achieved.
Stability, hydrodynamic, and propulsion analyses are also performed, with propulsion systems modified as needed (hull form remains fixed). Machinery, electrical, systems, piping, HVAC, cargo systems, and outfitting items are finalized. Comprehensive 3D models for structural, hydrodynamic, and electrical/machinery/piping aspects are created. The goal is to satisfy client requirements, minimize errors, optimize performance and safety, reduce steel weight, optimize construction costs, and prepare the design for production. Basic and detailed design are often combined in the contract design phase, signifying a commitment to the finalized design.
4. Production Design: From Blueprint to Reality
The final stage, production design, is conducted at the shipyard. It focuses on planning the actual construction and fabrication process, generating detailed working-level drawings (production drawings) with instructions for cutting, welding, erection, and installation. This stage includes schedules for all yard activities and clear work instructions for workers, ensuring the ship is built according to the established timeline and design.